The industry recognizes BFS technology as one of the most advanced aseptic filling technologies, as it eliminates contamination risks.
Fast, Safe, Flexible: Blow-Fill-Seal Technology from the Inventor
Over 60 years ago, Rommelag pioneered a new era of aseptic filling with the invention of Blow-Fill-Seal (BFS) technology. This innovation revolutionized the industry by combining the time-consuming processes of container production, filling, and sealing into a single, flexible, fully automated aseptic process, providing the highest safety in sterile production for the pharmaceutical industry.
Functionality of BFS
How Blow-Fill-Seal Technology Works
Blow
Pure polymer granules are extruded to form a tube, which is then formed into a sterile container using vacuum and sterile air.
Fill
The container is instantly filled with the liquid or semi-solid substance in precisely the right quantity.
Seal
Finally, the container is hermetically sealed.
aseptic
filling volume
units per hour
Benefits
Benefits of Blow-Fill-Seal
Designed for easy opening and precise dispensing, BFS containers enable safe and reliable applications.
From ampoules to bottles, with features like hangers, recessed grips, droppers, embossed or labeled, vented or non-vented withdrawal - BFS adapts to your individual requirements.
BFS is engineered to meet the strict regulatory standards of global health authorities such as the FDA, EMA, and ANVISA, ensuring compliance across various product categories and international markets. By using high-purity, additive-free polymers like LDPE, BFS containers meet the rigorous requirements of the European Pharmacopoeia.
Since there are no prefabricated containers to store, transport, clean, or sterilize, Blow-Fill-Seal technology simplifies your logistics and significantly cuts costs.
BFS containers don't break or shatter like glass, reducing injury risks and contamination from shards. Their impact resistance also lowers the risk of damage during transport.
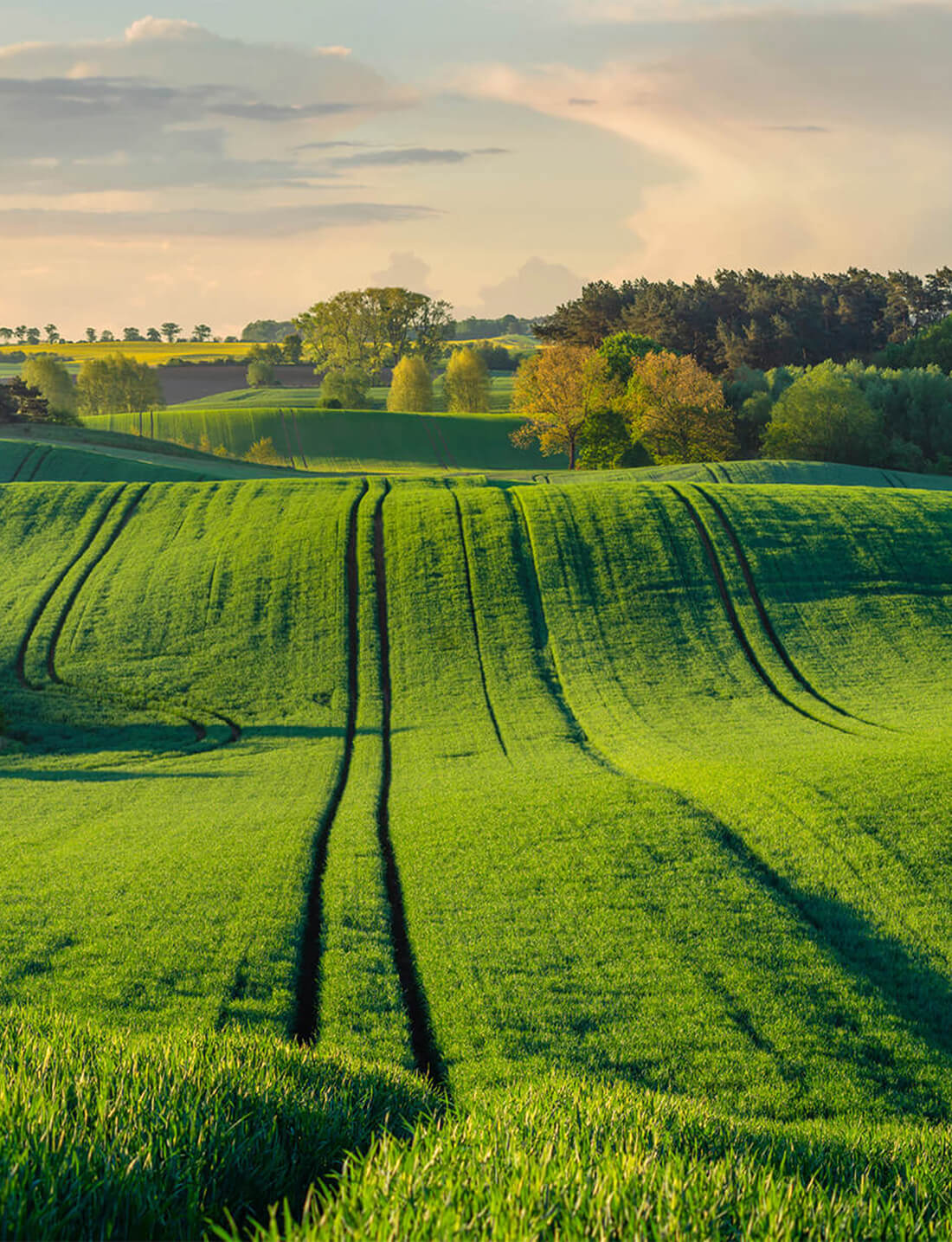
Sustainability
Sustainability Benefits of Blow-FIll-Seal
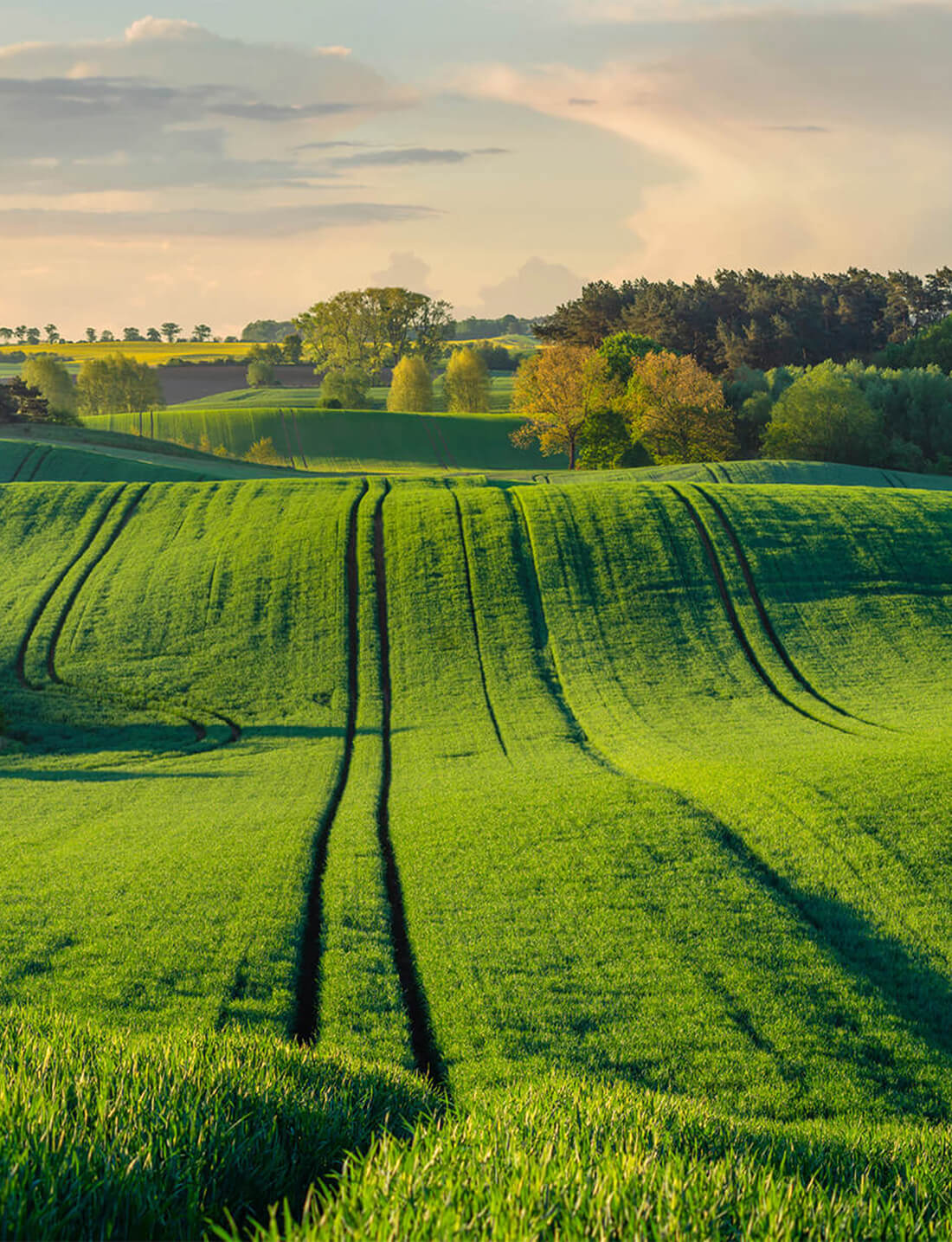
PRIMARY PACKAGING
Perfect BFS Primary Packaging for Every Application
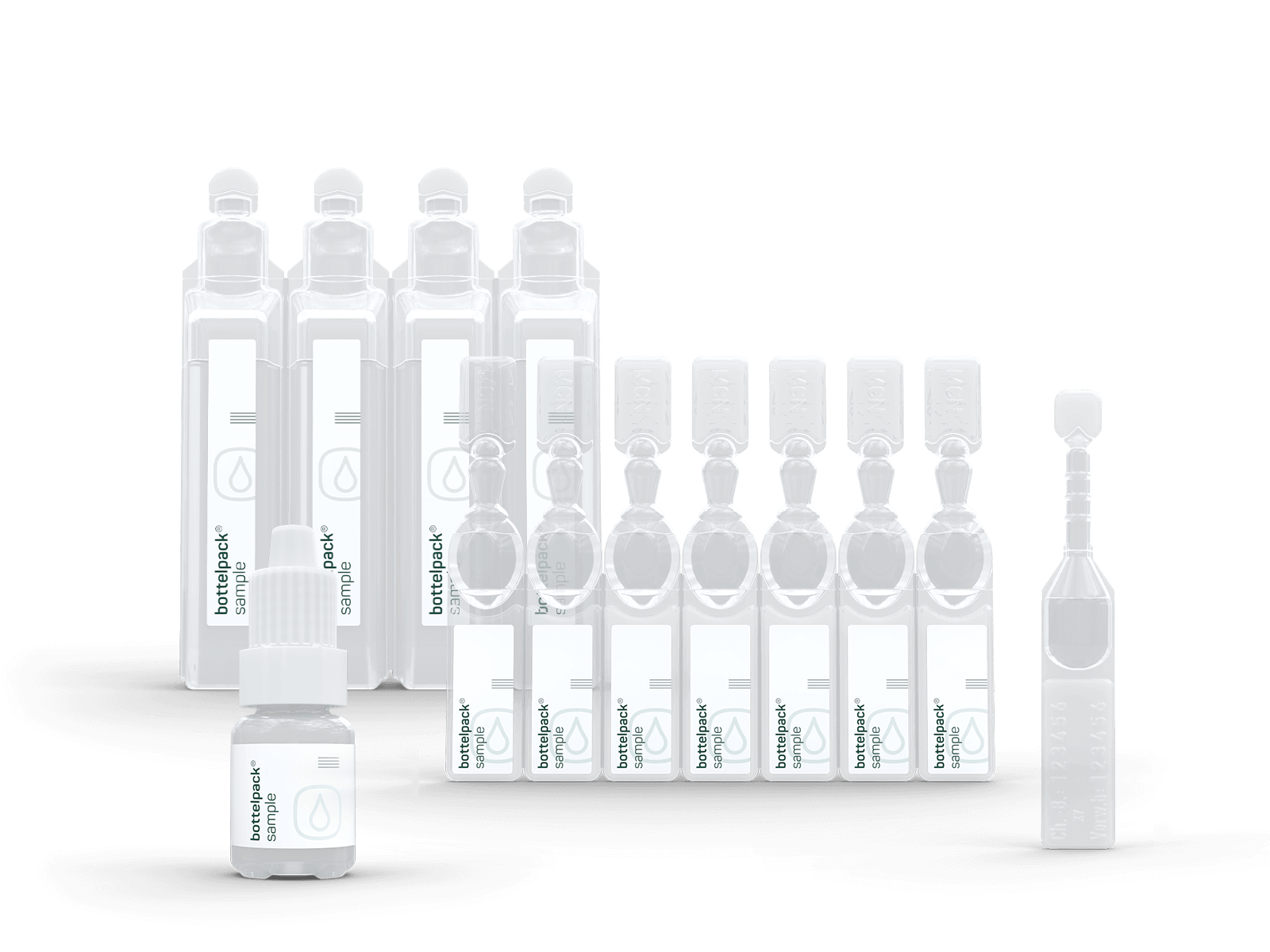
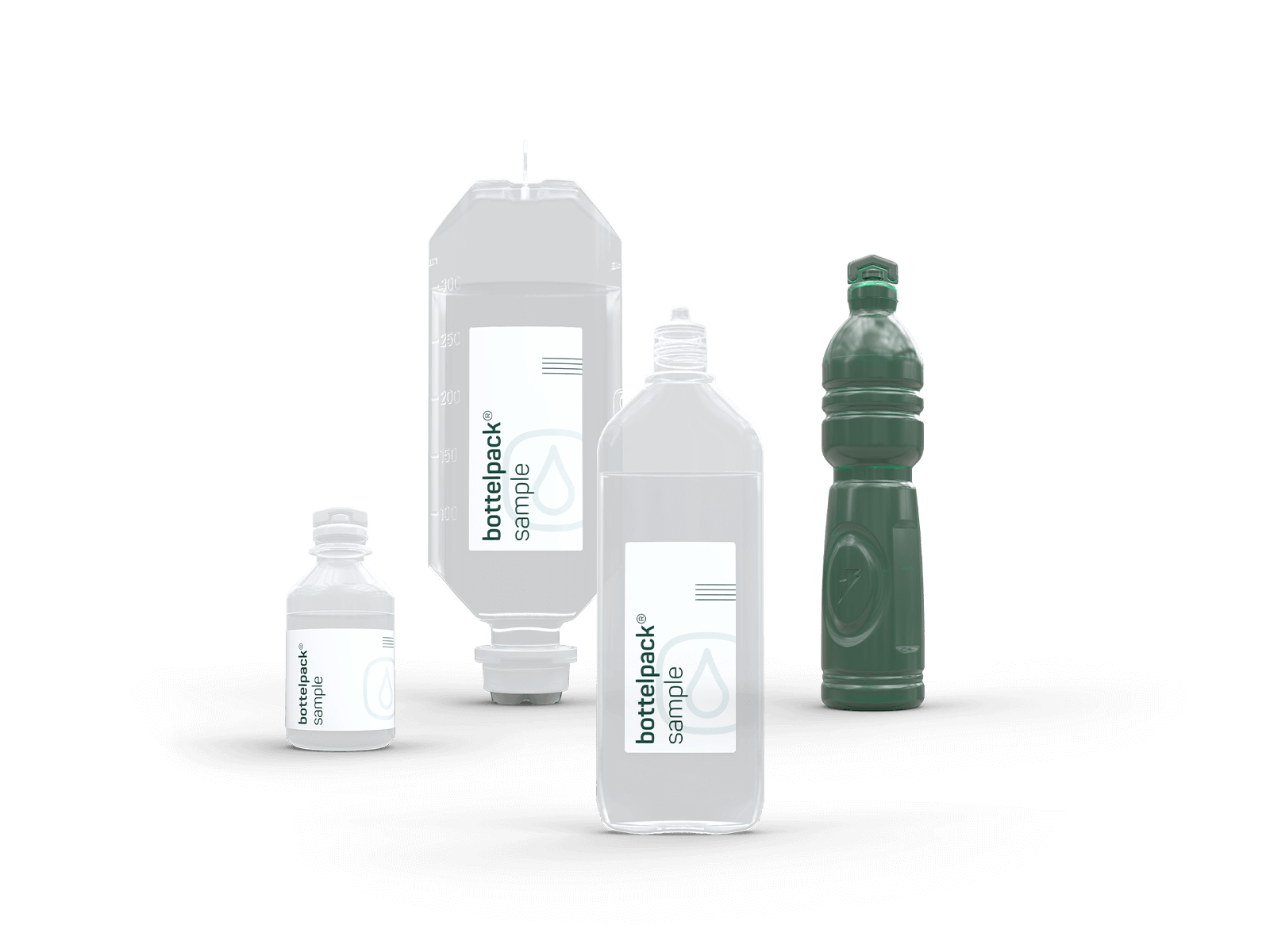
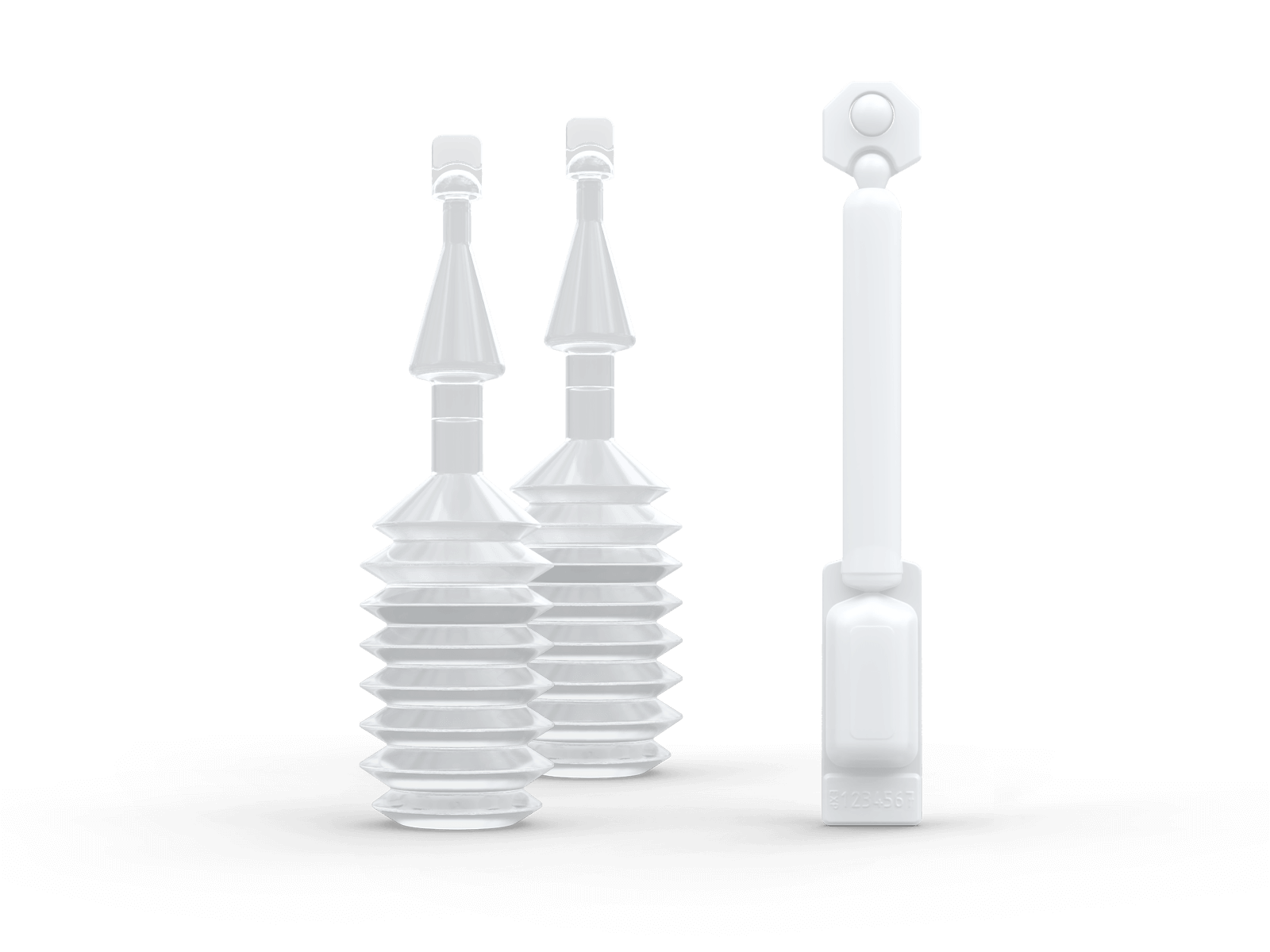
Connectors and Closures
Functional Connectors and Closures
Enables easy withdrawal of liquids using syringes without needing an additional needle. Ampoules with a vented Luer connection offer automatic pressure compensation, ensuring a smooth and consistent flow.
Formed directly during the sealing process, the twist-off cap is firmly attached to the container. Simply twist it to open. This method has been proven billions of times and offers highly flexible design options to meet diverse packaging needs.
The KME closure system features a screw cap with an integrated puncture pin. By twisting the cap into the bottle top, it creates an opening suitable for dripping or spraying, making it ideal for multi-use applications.
This closure system combines a sealed container with a Eurocap and is specifically designed to meet the stringent requirements of infusion bottles.
An alternative to Eurocaps, the nipplehead closure is formed during the sealing process, offering a different closure option to suit specific needs.
Multi-layered BFS
Excellent Barrier Properties with Multilayered BFS
If specific barrier properties are needed, BFS offers the option of a Coextrusion process. Our multilayer BFS containers achieve excellent barrier properties against water vapor and gas, protecting sensitive liquids from environmental factors.
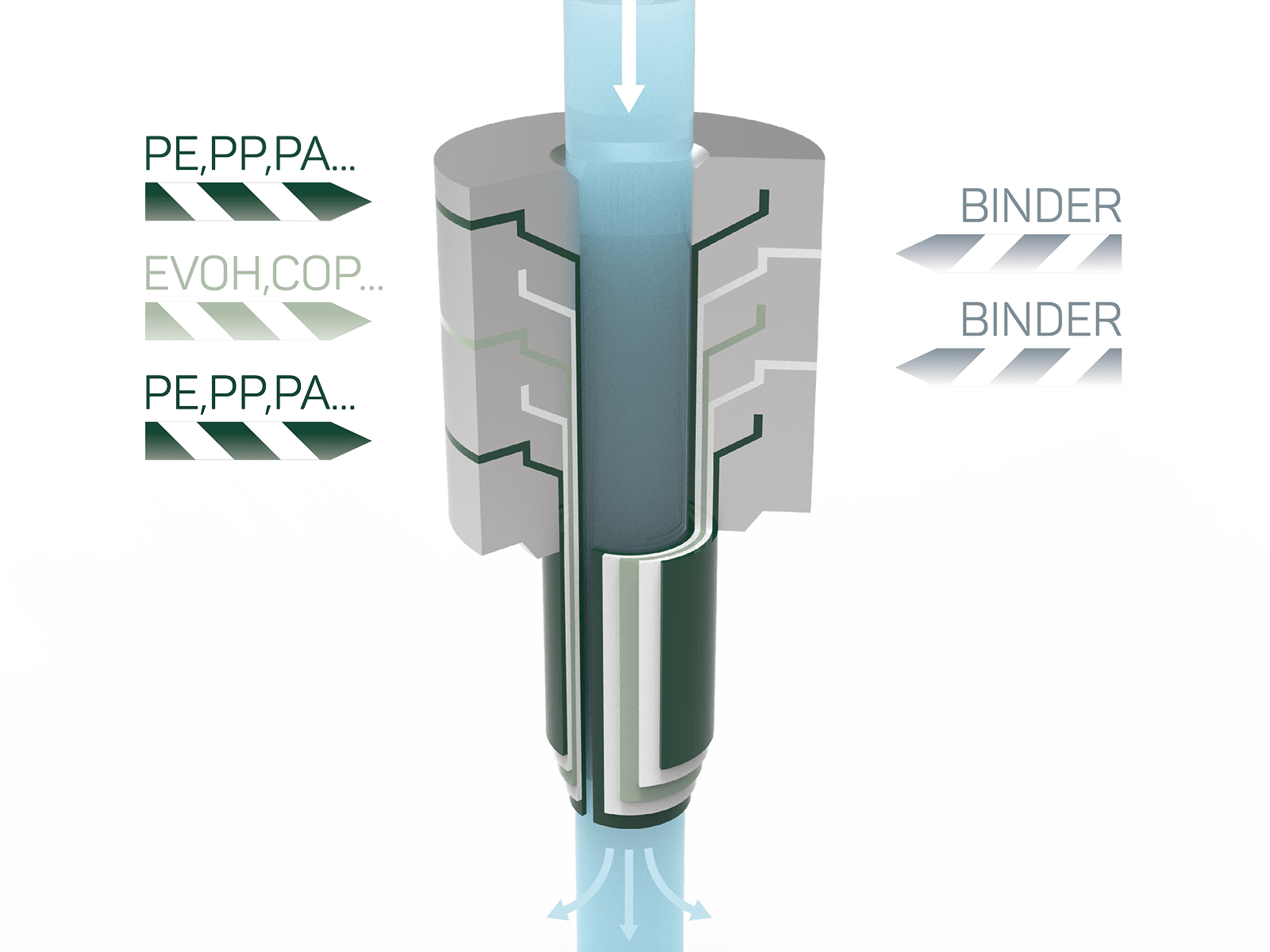
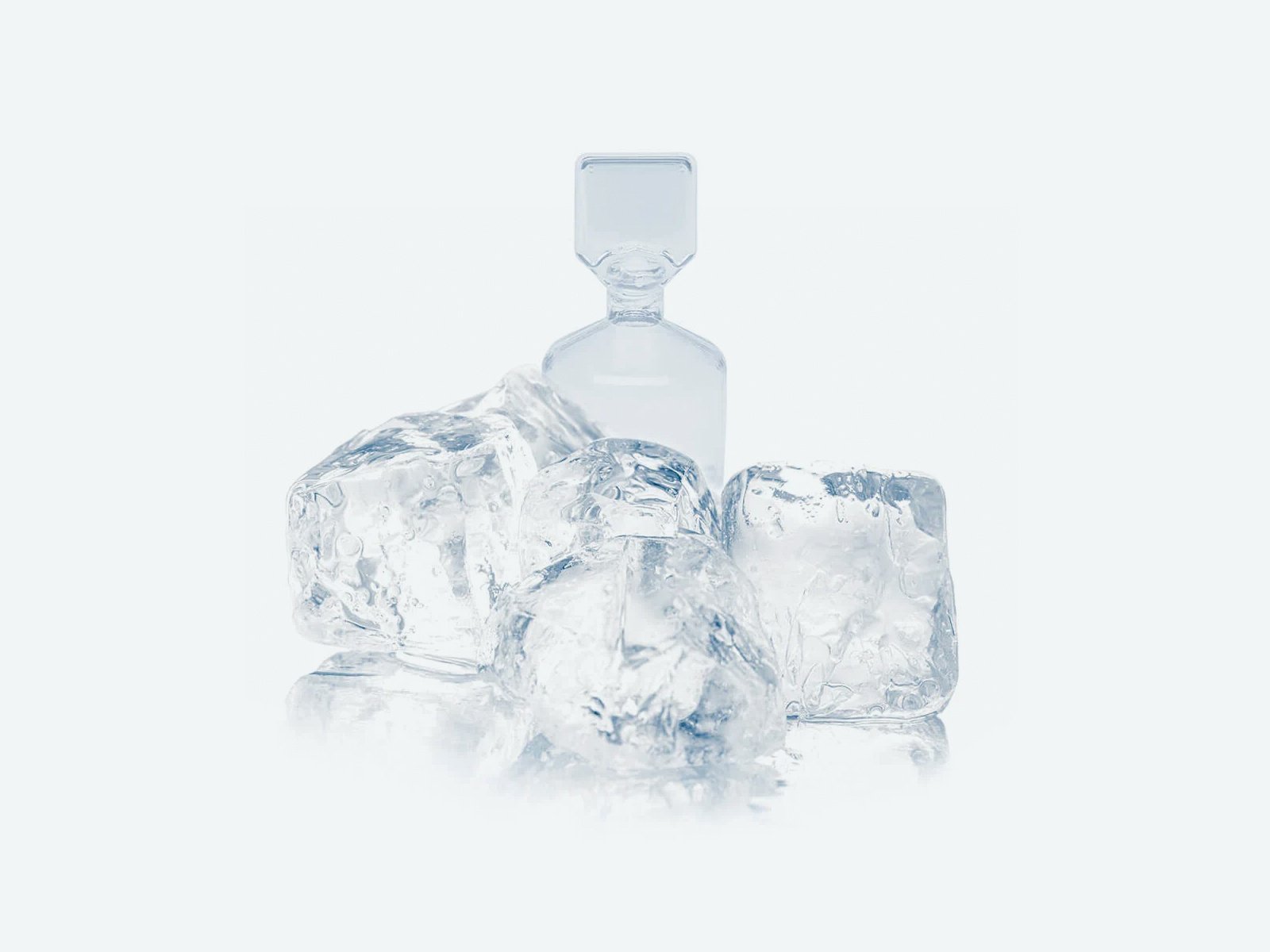
coolBFS
coolBFS for the Filling of Temperature-Sensitive Liquids
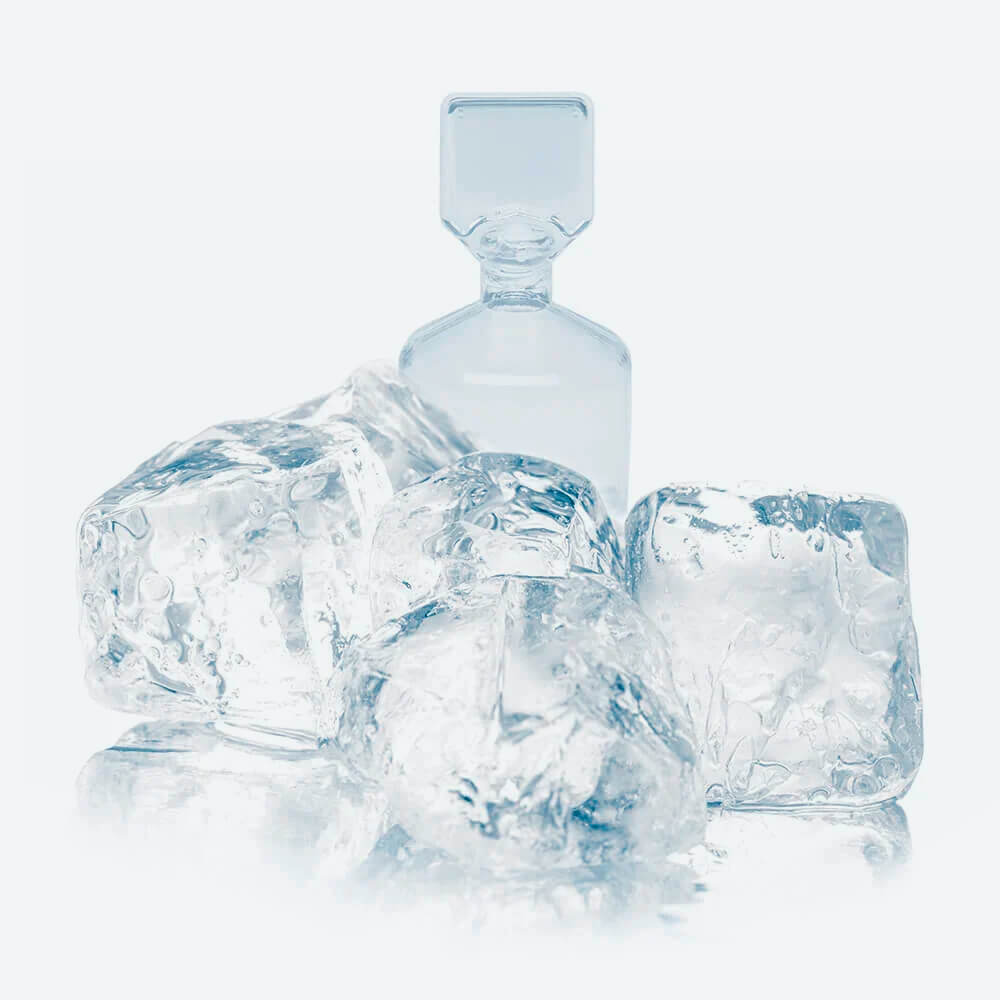
One-Stop-Partner
More Than a Machine Supplier—Your BFS One-Stop-Partner
We provide various options for integrating our Blow-Fill-Seal technology into your operations. Whether you're seeking to outsource production through our contract filling services or establishing your own in-house facilities with our bottelpack filling machines, we have a solution to meet your needs.
Furthermore, our experienced team is available to offer comprehensive support in developing and optimizing your product for BFS, ensuring a seamless transition from concept to market.